Introduction
Diesel generators play a vital role in providing backup power during emergencies and ensuring uninterrupted operations in various industries. To ensure that a diesel generator operates efficiently and reliably when needed, commissioning testing is essential. Commissioning testing involves a series of checks and assessments to verify the performance and functionality of the generator before it is put into service. This comprehensive guide will explore the importance of commissioning testing for diesel generators, the different types of tests involved, best practices to follow, and the benefits of conducting thorough testing.
Importance of Commissioning Testing for Diesel Generators
Commissioning testing is a crucial step in the installation and maintenance of diesel generators. It is a comprehensive process that involves testing various components and systems of the generator to ensure that it meets the required standards and specifications. By conducting commissioning testing, operators can identify any potential issues or defects early on and address them before the generator is put into service. This proactive approach helps prevent costly downtime, equipment failures, and safety hazards.
Commissioning testing also helps verify the performance characteristics of the diesel generator, such as its output capacity, efficiency, and response time. By testing the generator under different load conditions, operators can ensure that it will meet the power demands of the facility or system it is intended to support. Additionally, commissioning testing helps validate the functionality of safety features, control systems, and other critical components of the generator to ensure reliable operation during power outages or emergencies.
Types of Commissioning Tests for Diesel Generators
There are several types of tests involved in the commissioning process for diesel generators. These tests are designed to evaluate different aspects of the generator's performance and functionality. Some of the most common types of commissioning tests for diesel generators include:
1. Mechanical Inspection: This test involves visually inspecting the generator for any signs of damage, leaks, or wear and tear. It also includes checking the alignment of components, fasteners, and connections to ensure proper installation.
2. Diesel generator for military applications : Electrical testing involves verifying the voltage, current, frequency, and waveform of the generator output. This test ensures that the generator is capable of providing the required electrical power within acceptable tolerances.
3. Load Bank Testing: Load bank testing is conducted to simulate real-world operating conditions and test the generator's performance under different load levels. This test helps identify any issues with the generator's capacity, voltage regulation, and response time.
4. Fuel System Testing: Fuel system testing involves checking the fuel quality, fuel supply lines, filters, and injectors to ensure proper fuel delivery to the engine. This test helps prevent fuel-related issues that can impact the generator's performance.
5. Cooling System Testing: Cooling system testing involves checking the coolant level, temperature, pressure, and flow rate to ensure proper cooling of the engine. This test helps prevent overheating and ensures the longevity of the generator.
6. Control System Testing: Control system testing involves verifying the functionality of the generator's control panel, sensors, alarms, and safety features. This test ensures that the generator can be started, stopped, and monitored effectively.
Best Practices for Diesel Generator Commissioning Testing
To ensure a successful commissioning testing process for diesel generators, operators should follow best practices and guidelines. Some key best practices for diesel generator commissioning testing include:
1. Develop a Comprehensive Test Plan: Before starting the commissioning testing process, operators should develop a detailed test plan that outlines the scope of testing, test procedures, acceptance criteria, and responsibilities. A well-defined test plan helps ensure that all necessary tests are conducted and documented properly.
2. Follow Manufacturer's Recommendations: It is essential to follow the manufacturer's recommendations and guidelines for commissioning testing. This includes adhering to the recommended test procedures, safety precautions, and maintenance requirements specified in the generator's manual.
3. Conduct Pre-Commissioning Checks: Before conducting formal commissioning tests, operators should perform pre-commissioning checks to verify that the generator and associated systems are installed correctly and ready for testing. This includes checking electrical connections, fuel supply, cooling system, and control panel settings.
4. Perform Tests in a Controlled Environment: Commissioning tests should be conducted in a controlled environment with proper safety measures in place. Testing should be scheduled during non-peak hours to minimize disruptions and ensure the safety of personnel.
5. Document Test Results: It is essential to document the results of each test conducted during the commissioning process. This documentation should include test procedures, test data, observations, deviations, corrective actions taken, and acceptance criteria met.
6. Conduct Functional Testing: In addition to performance testing, operators should conduct functional testing to verify the proper operation of all control systems, safety features, alarms, and shutdown sequences. Functional testing helps ensure that the generator can be started, stopped, and controlled as intended.
Benefits of Conducting Thorough Commissioning Testing
Conducting thorough commissioning testing for diesel generators offers several benefits to operators and facility owners. Some of the key benefits of commissioning testing include:
1. Enhanced Reliability: By identifying and addressing potential issues early on, commissioning testing helps enhance the reliability of diesel generators. This proactive approach minimizes the risk of unexpected failures and ensures that the generator will perform as intended during emergencies.
2. Improved Performance: Commissioning testing helps verify the performance characteristics of the generator, such as its output capacity, efficiency, and response time. By conducting load bank testing and other performance tests, operators can ensure that the generator meets the power demands of the facility and operates efficiently.
3. Extended Equipment Life: Regular commissioning testing helps identify and prevent issues that can shorten the lifespan of diesel generators. By ensuring proper maintenance, testing, and monitoring, operators can extend the equipment life and maximize the return on investment.
4. Compliance with Regulations: Commissioning testing helps ensure that diesel generators comply with regulatory requirements and industry standards. By conducting tests to verify the performance and functionality of the generator, operators can demonstrate compliance with safety, environmental, and quality standards.
5. Minimized Downtime: By conducting thorough commissioning testing, operators can minimize the risk of unexpected downtime due to equipment failures or malfunctions. Identifying and addressing issues during testing helps prevent costly disruptions and ensures continuous operations.
Conclusion
Commissioning testing is a critical step in ensuring the reliability, performance, and safety of diesel generators. By following best practices, conducting thorough testing, and documenting results, operators can maximize the efficiency and longevity of their generators. The comprehensive guide provided in this article highlights the importance of commissioning testing, the types of tests involved, best practices to follow, and the benefits of conducting thorough testing. By investing time and resources in commissioning testing, operators can ensure that their diesel generators are ready to provide backup power whenever needed.
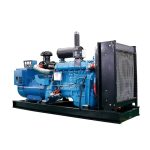